XGT Confirms Ultra-Pure Vanadium Oxide Process
- X GROUP Technologies
- Apr 14
- 3 min read
The new vanadyl process of X GROUP Technologies (XGT) delivers battery-ready vanadium electrolyte at less than 60% of the cost of conventional preparation methods.
This unique capability was demonstrated at small commercial scales, which moved into larger-scale commercial production in the final quarter of 2024 (see our previous post).
This included the following process steps:
Low-cost extraction of vanadium from a range of secondary resources,
Adsorption of vanadium onto ion exchange resin, for isolation, purification and concentration,
Modification of the eluate solution to correct vanadium molarity (1.8M), valence charge (50% V4+ and 50% V3+) and sulphuric acid matrix (40%), consistent with electrolyte specifications.
The ultra-pure vanadyl sulphate eluate offers the following advantages;
produces concentrated vanadyl sulphate solution directly off the IX process, for preparing VRB electrolyte,
the >2M vanadyl sulphate eluate requires only minor adjustments to acidity and electrolytic reduction from V4+ to V3.5+ (50% V3+ 50% V4+ as 1.8M V in 40% H2SO4) before placement within a VRB system.
preparing VRB electrolyte in a liquid-only flowsheet from vanadium recovered from secondary resources offers competitive advantages over primary production, where more costly premium-grade V2O5 and V2O3 are dissolved in sulphuric acid to prepare electrolyte.
In a further refinement of the vanadyl sulphate process, a complimentary capability was developed towards the end of 2023 for precipitating hydrated vanadium dioxide (chemical formula VO(OH)2).
Hydrated vanadium dioxide precipitate – wet and dried
The hydrate rapidly dissolves in 40% sulphuric acid at ambient temperatures, achieving up to 5M VOSO4 concentration in less than 30 minutes.
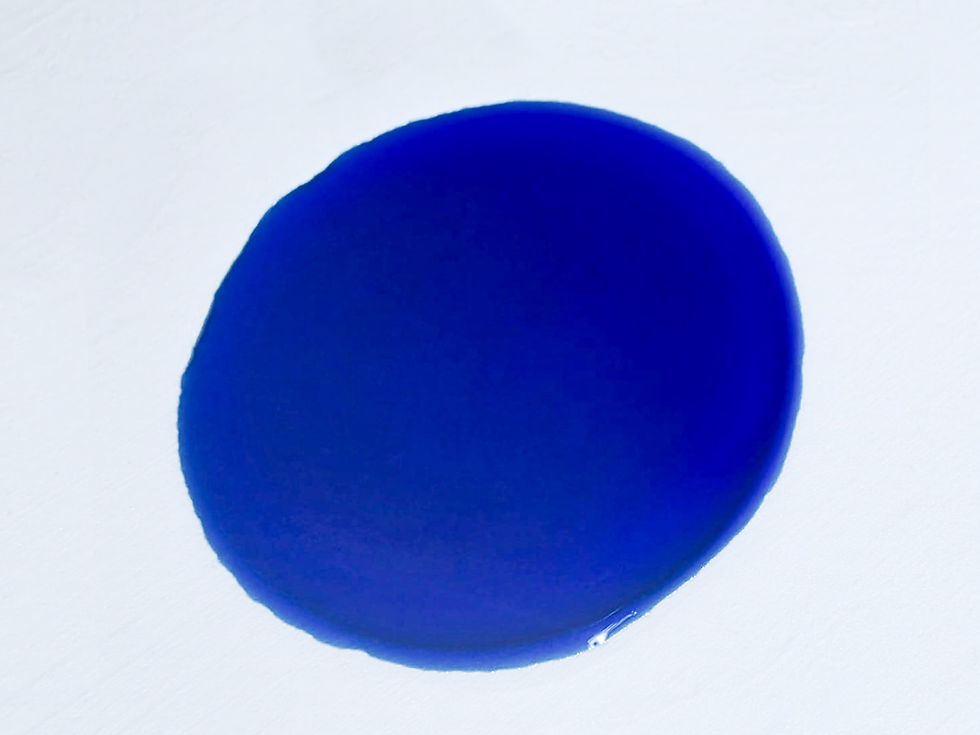
A pilot program was also completed on the conversion of the hydrate to high purity vanadium oxides V2O3, VO2 and V2O5.
Using the conventional roasting method (above 500°) under atmospheric conditions, the VO2 hydrate is converted to the V5+ compound vanadium pentoxide (V2O5). This oxide is suitable for super alloys and aerospace, for crafting turbine blades, jet engines and other fast-moving components exposed to high temperatures as well as preparing vanadium electrolyte.

Roasting under hydrogen at higher temperatures (above 800°C), reduces the vanadium to V3+, resulting in vanadium trioxide (V2O3). This oxide is used as a catalyst in various chemical processes such as ethanol production from ethylene. It is also used in ferrovanadium and vanadium aluminium alloys as well as the preparation of vanadium electrolyte for energy storage.
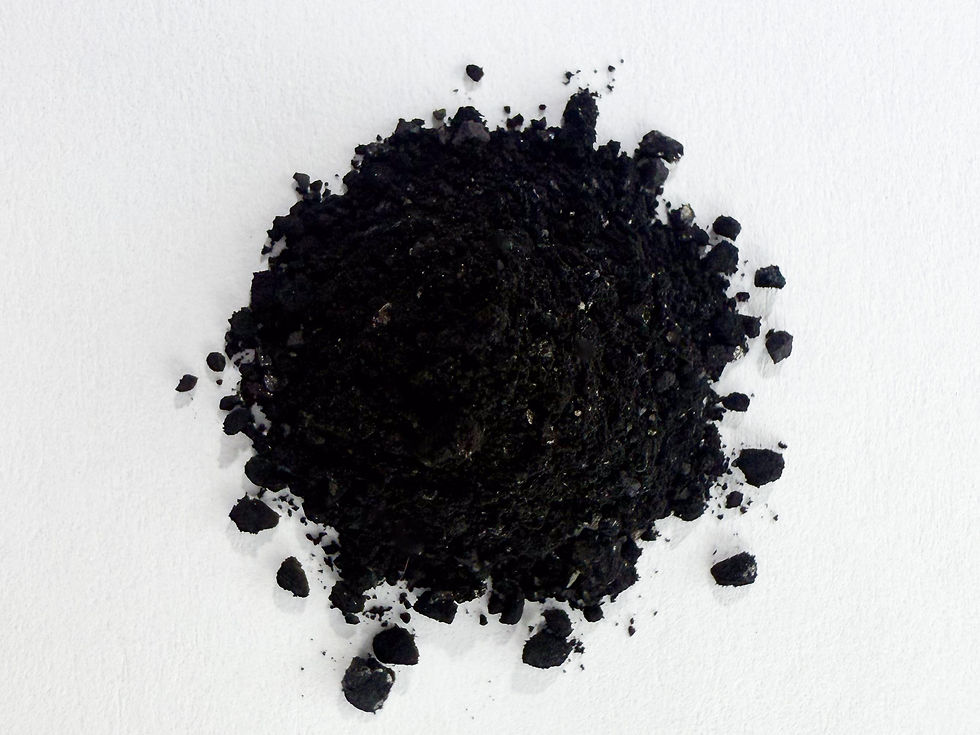
Roasting under nitrogen at lower temperatures (below 500°C) converts the hydrate to vanadium dioxide (VO2). This is used in “smart” materials, energy storage, and various other technologies due to unique properties of this material. VO2 can undergo the reversible-metal-to-insulator transition, suitable for certain electronic sensors and use on “smart” windows which allows retention or release of heat within buildings to improve temperature control.
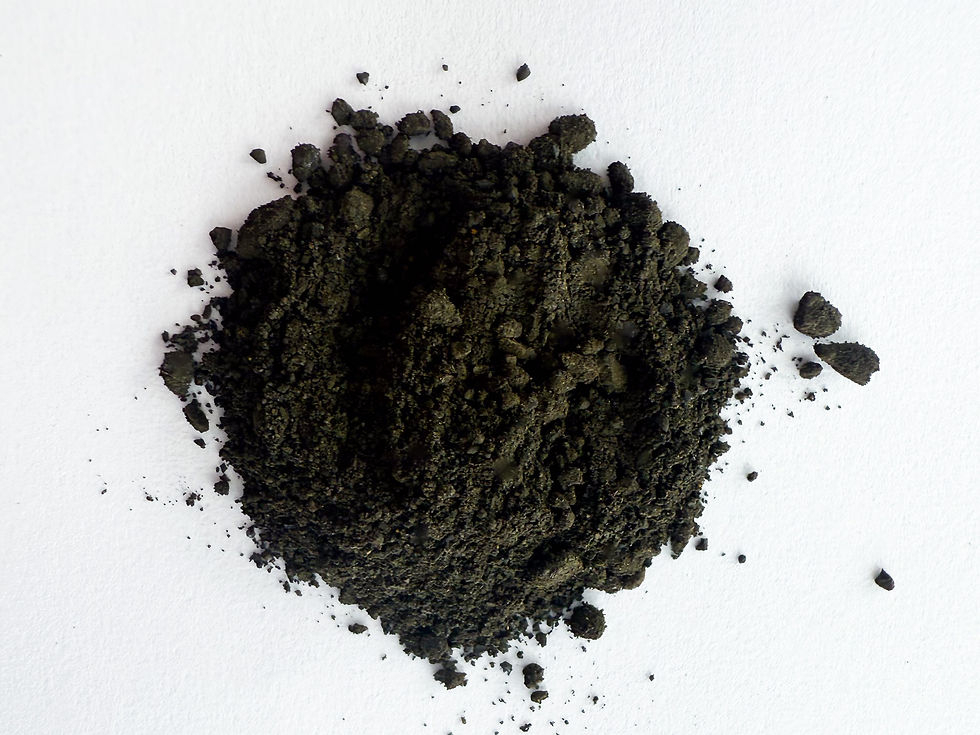
The low-cost hydrate process of XGT is well positioned to replace ammonium precipitation in primary production, considering the compelling advantages over conventional approaches;
lower capital and operational costs
improved water and salt balance in the extraction circuit, allowing recycling of the ammonium-free IX barren effluent directly to leach and treating only a portion of the leaching volumes for salt recovery
sulphur dioxide use in the purification process creates opportunity for recycling hazardous gas emissions from ore roasting
less onerous environmental compliance requirements from zero ammonium and sulphur dioxide emissions
superior finished goods purities open access to niche markets
The XGT team is making significant strides in developing vanadium oxides for superalloys applications as well as battery-ready vanadium electrolyte at a fraction of the cost of conventional methods, setting the stage for an exciting path forward.
Comments